The Makers: Prototyping Construction Tools
In this article, you will learn how students, as a part of a design option studio at the New Jersey Institute of Technology led by Professor Andrzej Zarzycki, utilized robotic fabrication techniques for construction in the Fall of 2019.
Robotics and automation are redefining the construction industry by streamlining labor-intensive tasks and sheltering humans from unhealthy and dangerous working conditions. From building demolition and tile-laying helpers to large 3D printing automatons producing mass-customized designs, robots deliver efficient and innovative outcomes. Robots also extend our faculties—mental and physical. They are creative tools that transform the ways we conceptualize architecture and provide an opportunity to redefine the very nature of the built environment. Therefore, it is critical that architecture students, and architects in general, explore opportunities associated with robotic technologies. The student work presented below exemplifies curricula that respond to these emerging autonomous construction and intelligent building frameworks.
Studio Description
This design option studio, “Robotic Fabrication and Assembly Processes: Prototyping Construction Tools,” investigated strategies for robotically assisted construction processes combining conventional and emerging material technologies. Specifically, it focused on designing and prototyping the task-specific robotic end effectors (custom fabrication tools) for the ABB 4600 2.55 m 7-axis (including 20-foot rail) robotic arm with an IRC5 single controller. Students worked with embedded components (sensors, actuators, and microcontrollers) to design automated toolsets capable of performing dedicated construction assembly and/or fabrication tasks. These tasks mimicked human-labor abilities and proposed novel ways of assembling architecture. Students used these custom-designed end effectors with the robotic arm to produce simple construction assemblies to validate their ideas. The outcomes of the studio included a series of construction assemblies produced with student-designed end effectors, functional prototypes of the end effectors, and documentation of the data-driven prototyping processes.
Design teams:
Brick Laying Smart Gripper: William Hall, Jalaysia Stevenson, and Meraj Nasi
Clay extruder: John Braun, Renzo Eseo, and David Skup
Additionally not shown here:
Plaster extrusion: Heesang Jung and Evelin Taipe
Plaster and concrete Injector: Vincent Hu and Patrick Quinn
Facade panel thermoformer: Ramez Hanna, Angela Micevska, and Steve Vivar
Tile laying: Sandy Hanna, Justin Melao, and Edgard Rodriguez
Robotic Fabrication and Assembly Processes: Prototyping Construction Tools
Bricklaying End Effector
The team’s interest in working on a conventional brick assembly using unconventional tools and techniques originated from the observation that bricklaying jobs are highly labor demanding, with a significant impact on workers’ health and well-being. To expand on the current state of robotic construction approaches, not to replicate it, the team proposed the integration of various sensors with a conventional pneumatic gripper approach.
The project team, Jalaysia Stevenson, Meraj Nasi, and William Hall, developed two brick gripper modules that integrated (1) an RGB color sensor (TCS34725) and (2) a radio frequency identification (RFID) sensor. These end-effector enhancements allowed for targeted selection and manipulation of bricks and construction components by allowing users to recognize and track individual elements by referring to their color or to an associated RFID tag. Individualized tracking allowed robots to respond in real-time to “site” conditions.
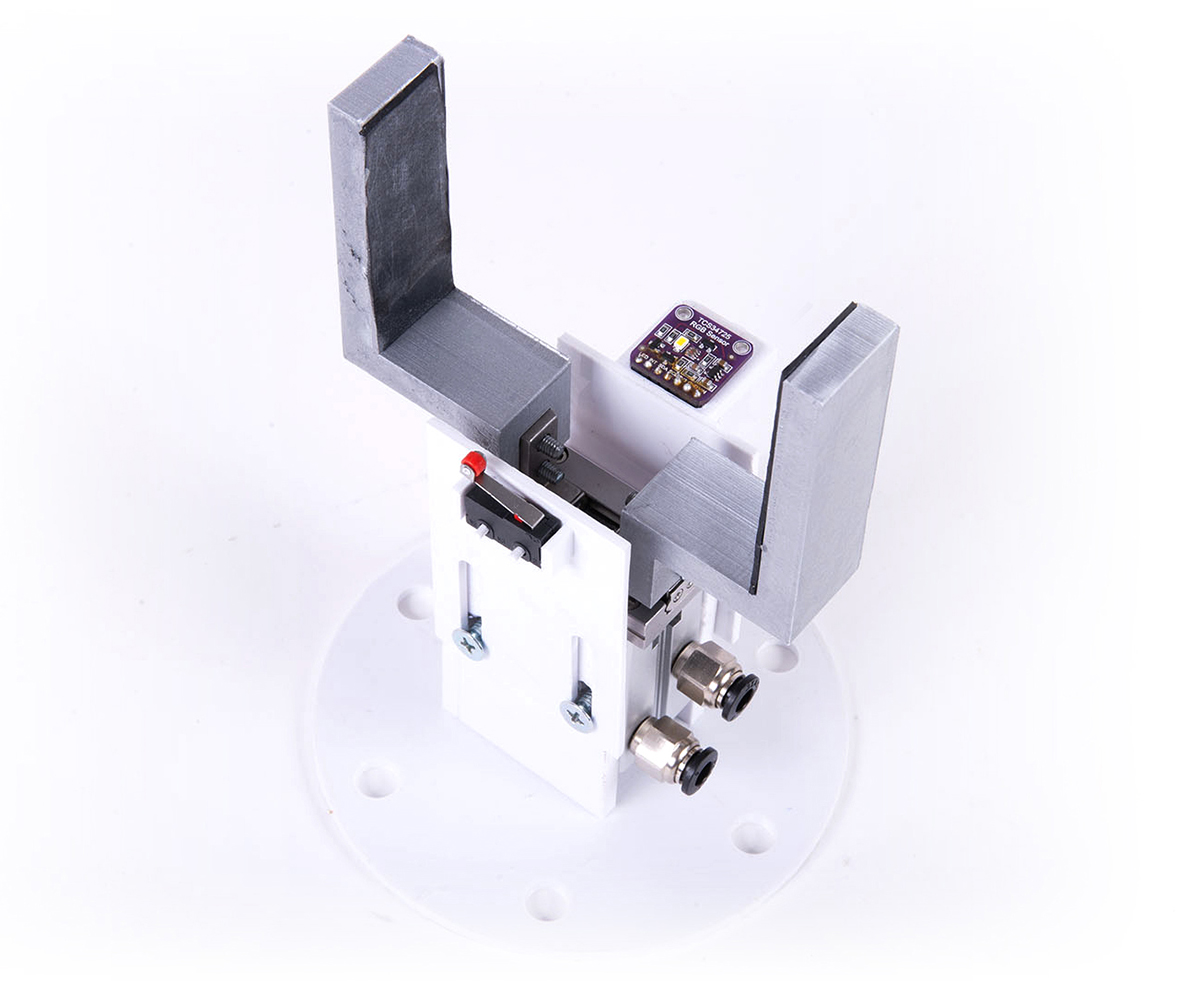
Custom-designed RGB color-sensing pneumatic brick gripper
Students Jalaysia Stevenson, NJIT’21 (left), and Meraj Nasi, NJIT’21 (right), discuss their design for the color-sensing bricklaying end effector. The TCS34725 RGB sensor allows the robotic arm to recognize components of a specific color or range of colors.
A TCS34725 RGB color sensor was used to enable the gripper to distinguish between different brick colors using a Kelvin color temperature scale. Students tested various color chips to set up appropriate tonal ranges for bricks.
The end effector deployed on the ABB 4600 robotic arm demonstrates the color-based gripper actuation. An RGB color sensor controls an actuation of the smart gripper. The reddish color is set to trigger the pneumatic actuator. Other colors will not actuate the end effector.
Wooden brick gluing and stacking
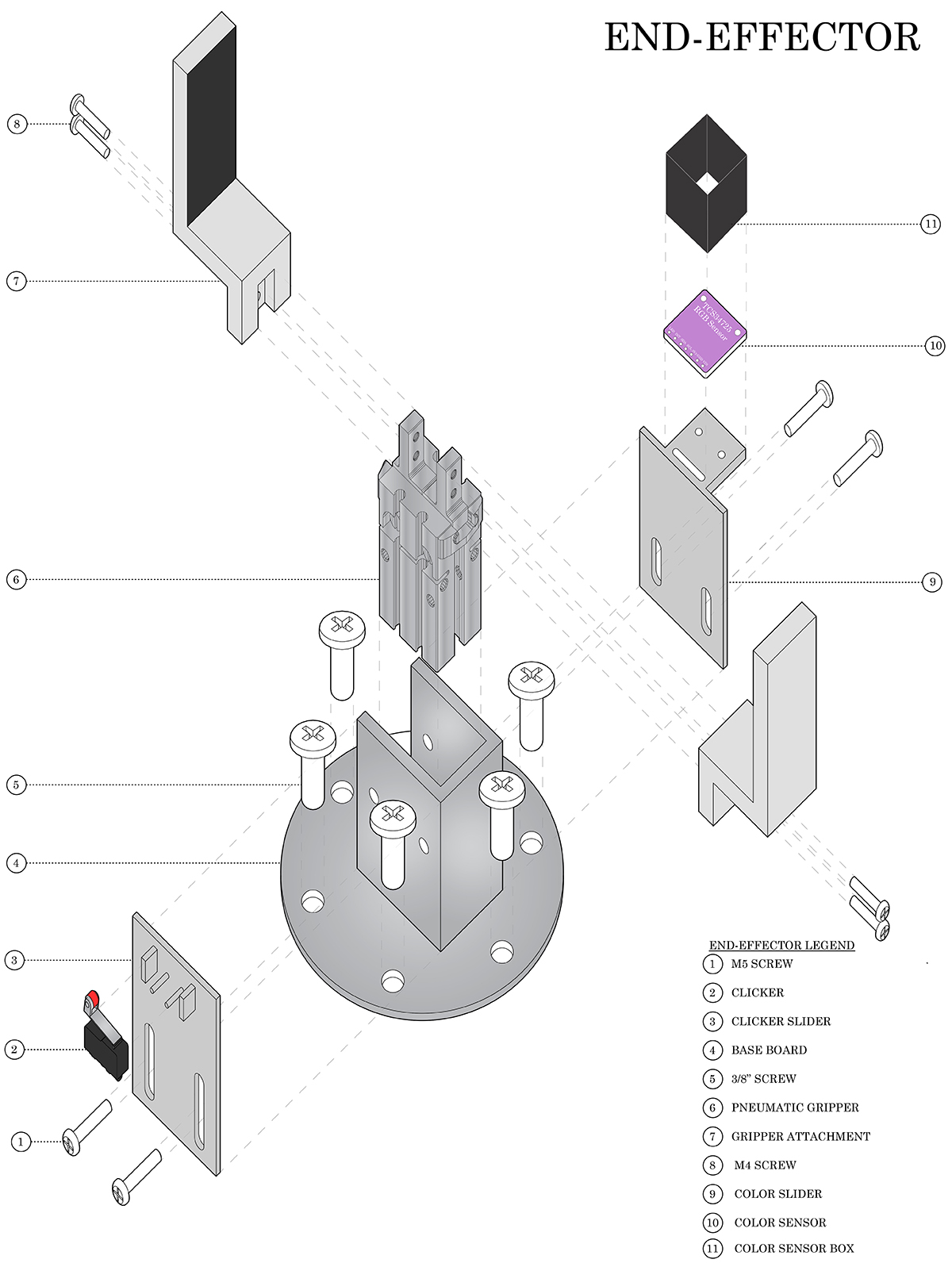
Exploded view of the color-sensing robotic gripper
Clay-Extruding End Effector
The project team, John Braun, Renzo Eseo, and David Skup (NJIT’20), have developed a pneumatically powered clay extruder (3D-printing) end effector. The end-effector development process involved a wide range of testing, including (1) air pressure and robot arm speed ratio; (2) various types, lengths, and diameters of extrusion head; and (3) moisture and plasticity of clay material. All tests were logged in a database and analyzed to identify the most promising clay extrusion scenarios. Two clay types were used for panel extrusions, with Buff Stoneware Clay No. 46 (Cone 5) as the primary material due to its superior plasticity and Terra Cotta Stoneware Clay No. 77 (Cone 5) as an alternate. Cone 5 clay was selected based on the desired application and clay firing procedures. After multiple tests, the team established that the Buff Stoneware Clay was easier to work with and provided more consistent results while extruding and drying.

Assembly and components of the pneumatic clay-extruding end effector
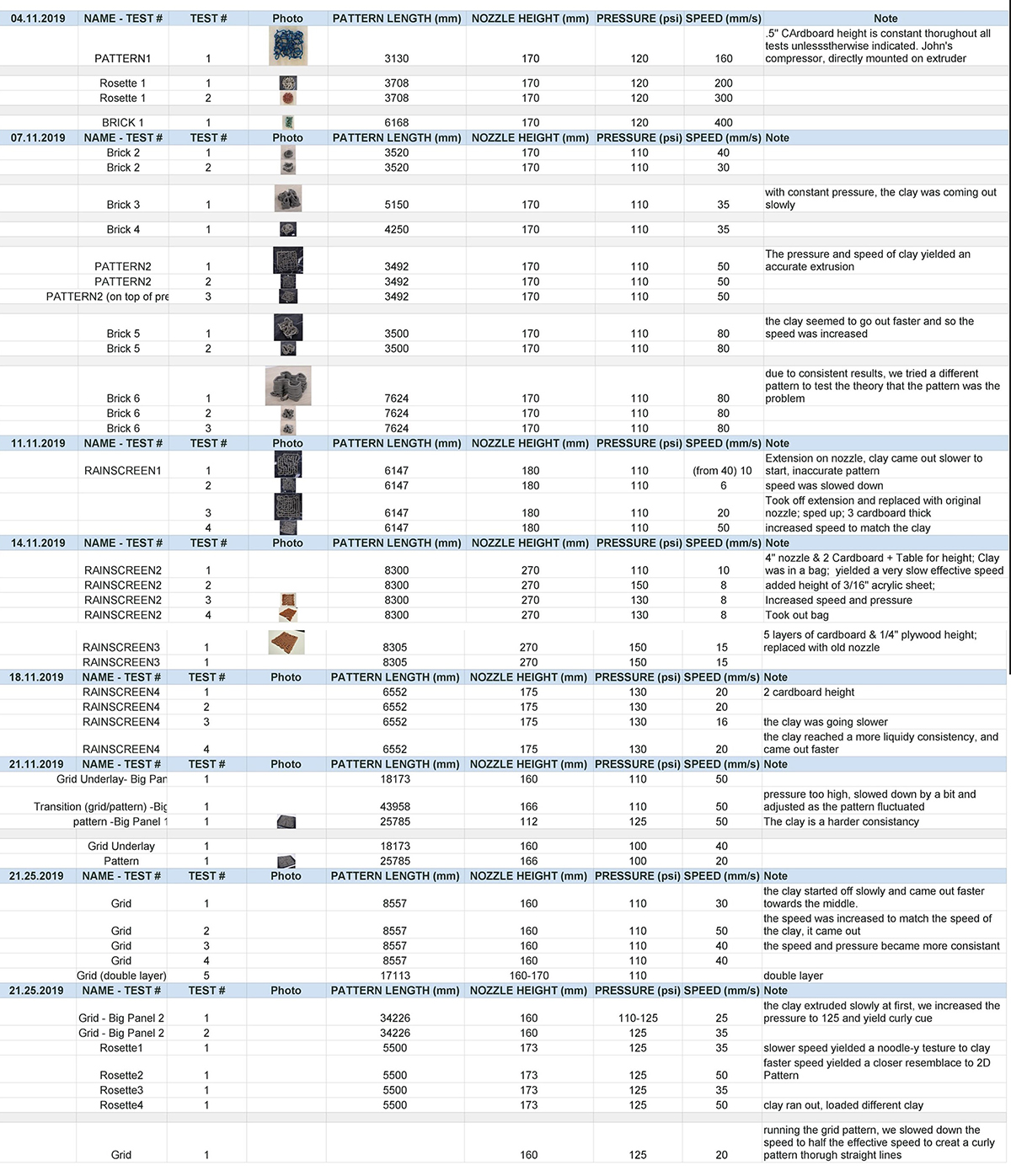
Tests were logged and annotated with parameters used for the extrusions. This was a critical part of the development process and successful outcomes.

A double-printed ceramic panel demonstrates the level of consistency achieved during clay extrusions. This technique was subsequently used in larger panels to increase their strength.
The first step in preparing for a clay extrusion exercise was to level the printing bed and test the pattern with a ball pen.
A single-layer clay extrusion utilizing an interlocking pattern to increase the structural strength and to reduce panel’s deformations associated with the initial drying of the raw clay material.
A clay-extruding head close-up, showing the speed and relative distances between the depositing tip and the panel base.
Final Thoughts
Engaging in robotic construction can be both exciting and intimidating. While it provides students with a direct and immediate authorship/execution of their designs—a strong sense of accomplishment–it also requires them to engage in creating-making with a high level of scientific rigor, to risk failure, and to learn skills not typically associated with architectural design studios. While the process can be frustrating, it is also rewarding and transformative.