Greg Spaw on Digital Fabrication at AUS
In the last decade, technology has shaped the way designers create, from the way they draw to the way they build. Now, designers can take an idea, draw it on their computer, and print out a 3D physical prototype with the aid of CAD/CAM (computer-aided design and computer-aided manufacturing) systems. All over the world, architecture schools have been steadily integrating these technologies into their curriculum.
Study Architecture invited Gregory Spaw to talk about a course he recently taught at the American University of Sharjah called Introduction to Digital Fabrication. While some of you out there may be advanced digital craftsmen, we thought it would be helpful to drill down (CNC pun intended) to find out what happens behind the scenes.
Tell us about teaching, “Introduction to Digital Fabrication”.
GS: The course had ten students at diverse levels of the program, from second through fifth year. They were assigned four projects over the semester and given about three weeks to complete each. Each project explored a different digital fabrication technique; and the students had to learn and demonstrate specific techniques associated with each of them.
Describe the projects that you selected. How did you choose the them?
GS: In this course, the students’ researched digitally fabricated projects which introduced a broad spectrum of skills and toolsets. With the elective free of prerequisites, the real challenge was creating projects that could accommodate a group of students with a wide range of experience with the equipment and techniques. I wanted them to gain fundamental skills while pursuing their own earnest design agendas. As the semester progressed, the complexity of the projects evolved, as did the techniques such as sectioning, folding, watertight digital modeling, to contouring and mold-making.
What were the learning objectives?
GS: Throughout the semester, emphasis was placed on iterative design and the use of physical testing to better understand processes of fabrication and material limitations. Students quickly discovered the value of both in the creation of their physical artifacts. The constant testing also gave the them a much better idea of material and fabrication tolerances which will, no doubt, inform their future design endeavors.
Which tools did you use?
GS: We are fortunate to have amazing analog and digital fabrication facilities at the American University Sharjah at our disposal, and so the students were able to use small format laser cutters, Kern HSE 400w large format laser (for cutting mild steel and stainless), filament and gypsum based 3D Printing, 3 axis CNC milling, and thermoforming for making molds.
Walk us through the process of each project.
Project 1: Fruit Bowl
Coming into the seminar, the students are generally comfortable with small format laser cutting of chipboard, museum board, and acrylic. The first project takes advantage of this familiarity and asks the students to use sectioning to create a fruit bowl. In support of the exploration, we introduce computation techniques in Rhino and Grasshopper. Students are also given a tutorial in RhinoNest to facilitate expedient labelling and laying out parts of their design for efficient cutting. Knowledge of this plug-in not only helped with the fruit bowl but also came in handy for the second project.
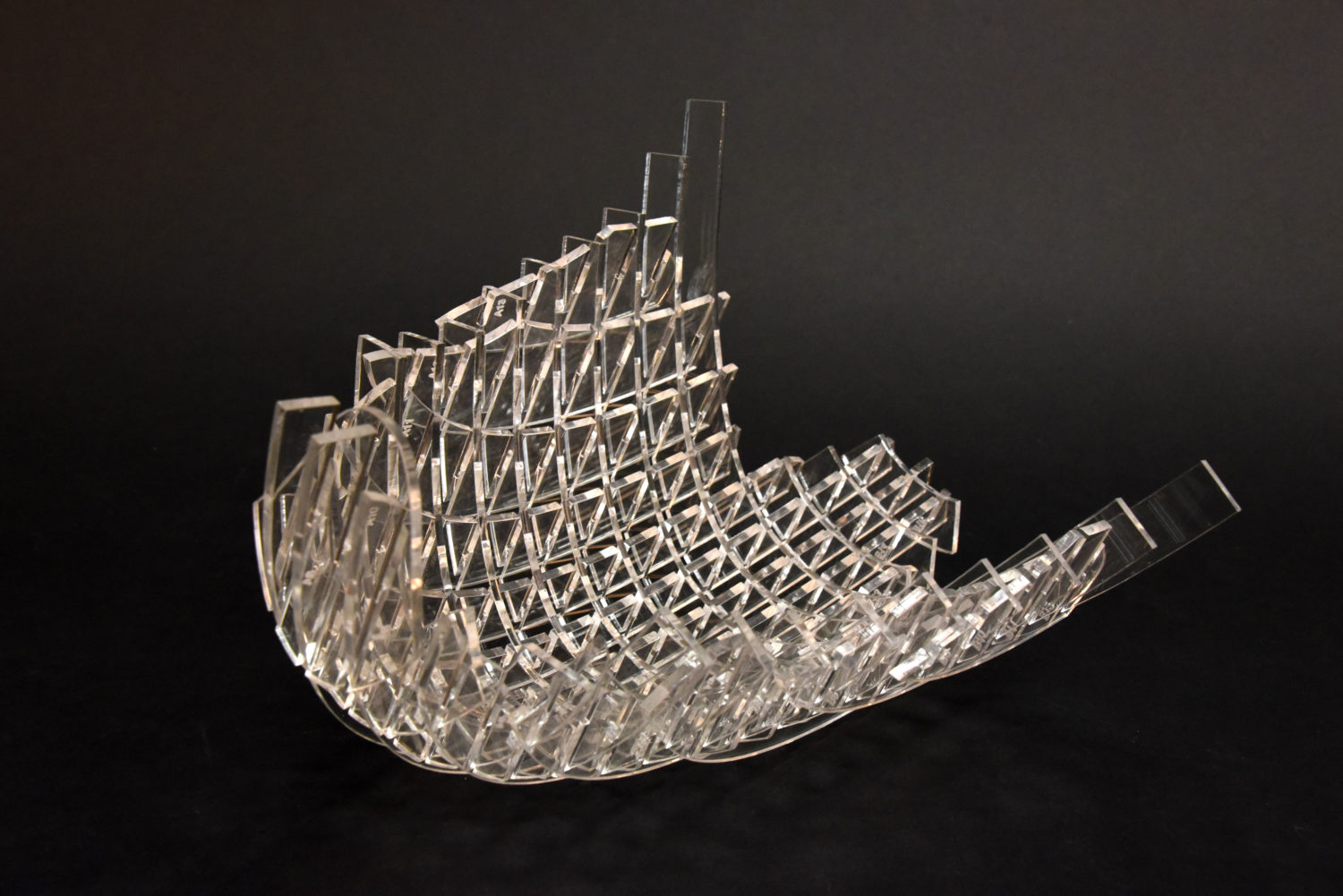
Fruit Bowl by Meera Aldarmaki
Project 2: Light Fixture
Building on the experience of the previous assignment, the second project asks students to use folding techniques in conjunction with thin gauge mild steel or stainless steel to create a lighting diffuser. This filter is designed to work with a standard, store-bought light bulb. After the design is complete, as-built drawings (drawings documenting the final design) of the students’ select fixture provided an opportunity for them to use digital calipers to create highly accurate digital models. It also forces them to confront questions of design and material tolerances. For this project, they use the school’s Kern HSE 400w large format laser, which is operationally similar to its smaller brethren, but harnesses greater power for cutting steel. In the process of completing the project, students also explore connections and finishes related to sheet metal.
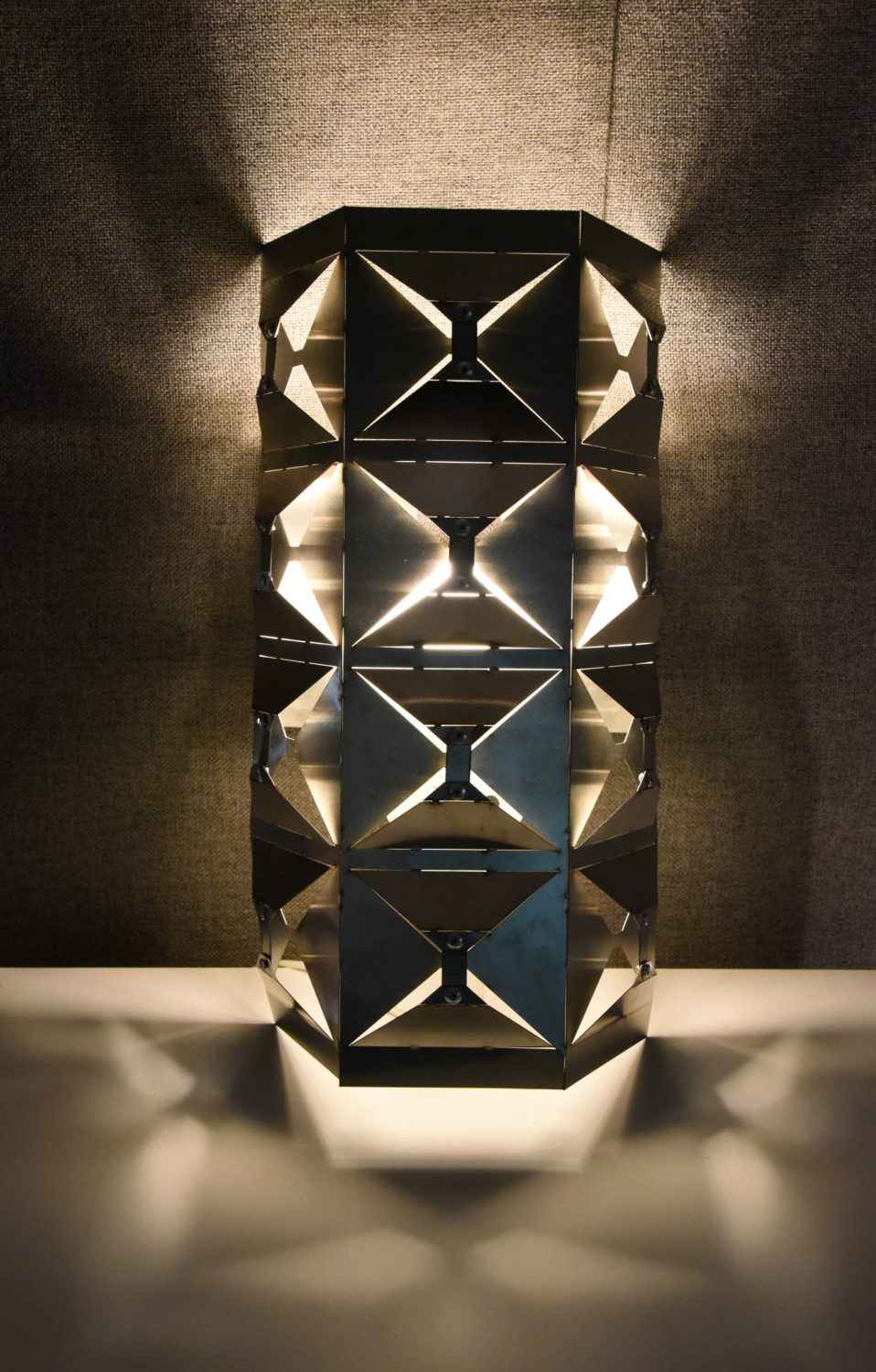
Light Fixture by Misbah Shehreen + Hidayathullah Baig
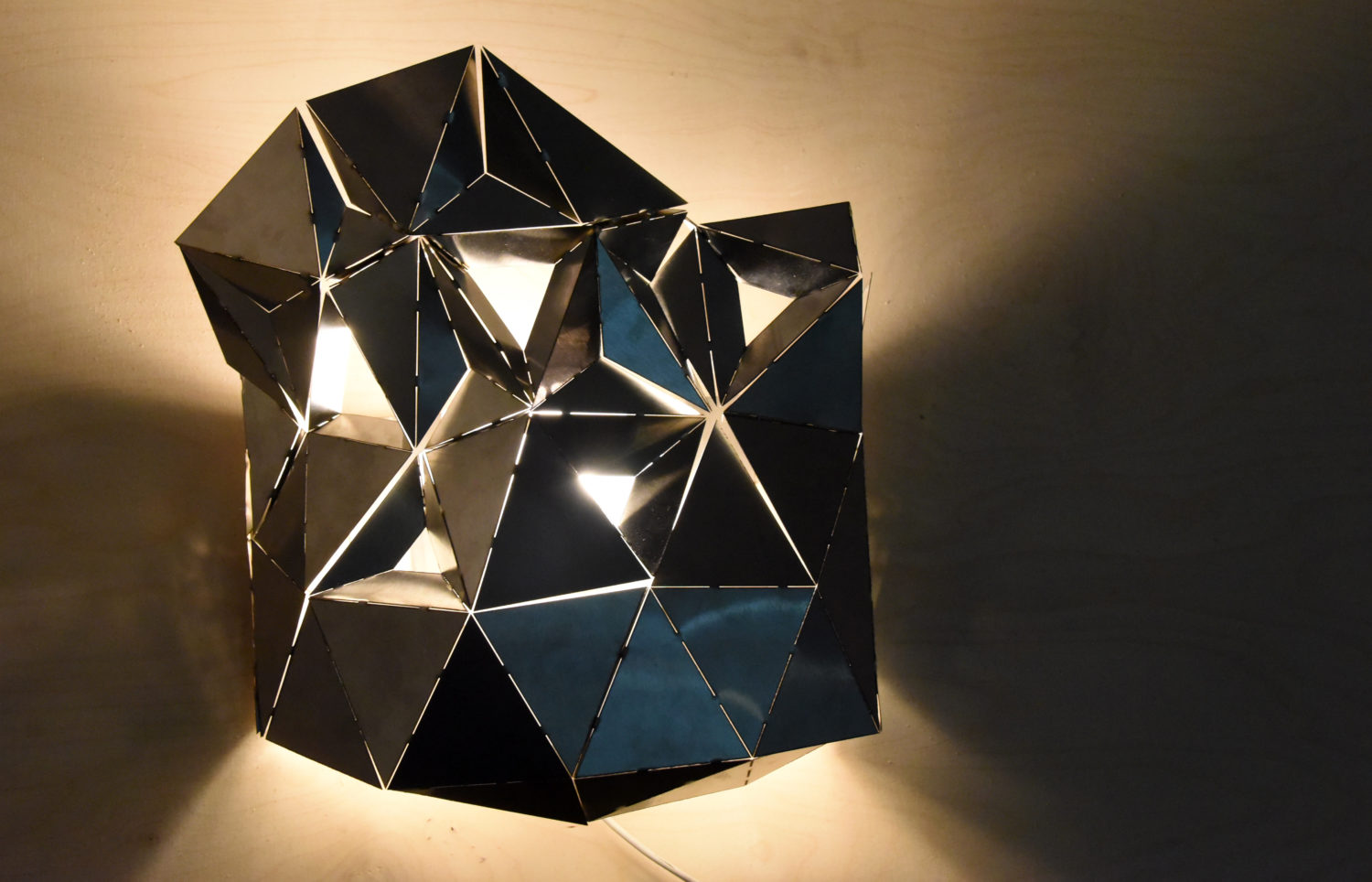
Light Fixture by Nermin Hagazy
Project 3: Spice Grinder
The third project asks students to design ergonomically-minded 3D-printed spice grinders, one that responds to the hands of the person using it. Accuracy in digital modeling is once again emphasized to first ensure watertight models necessary for the additive fabrication technique, and second to house an off the shelf ceramic grinding mechanism. Unlike the previous exercises, students are unable to physically test their designs because of availability and expense. With this in mind, additional foresight by the students is essential in order to avoid unintended surprises.
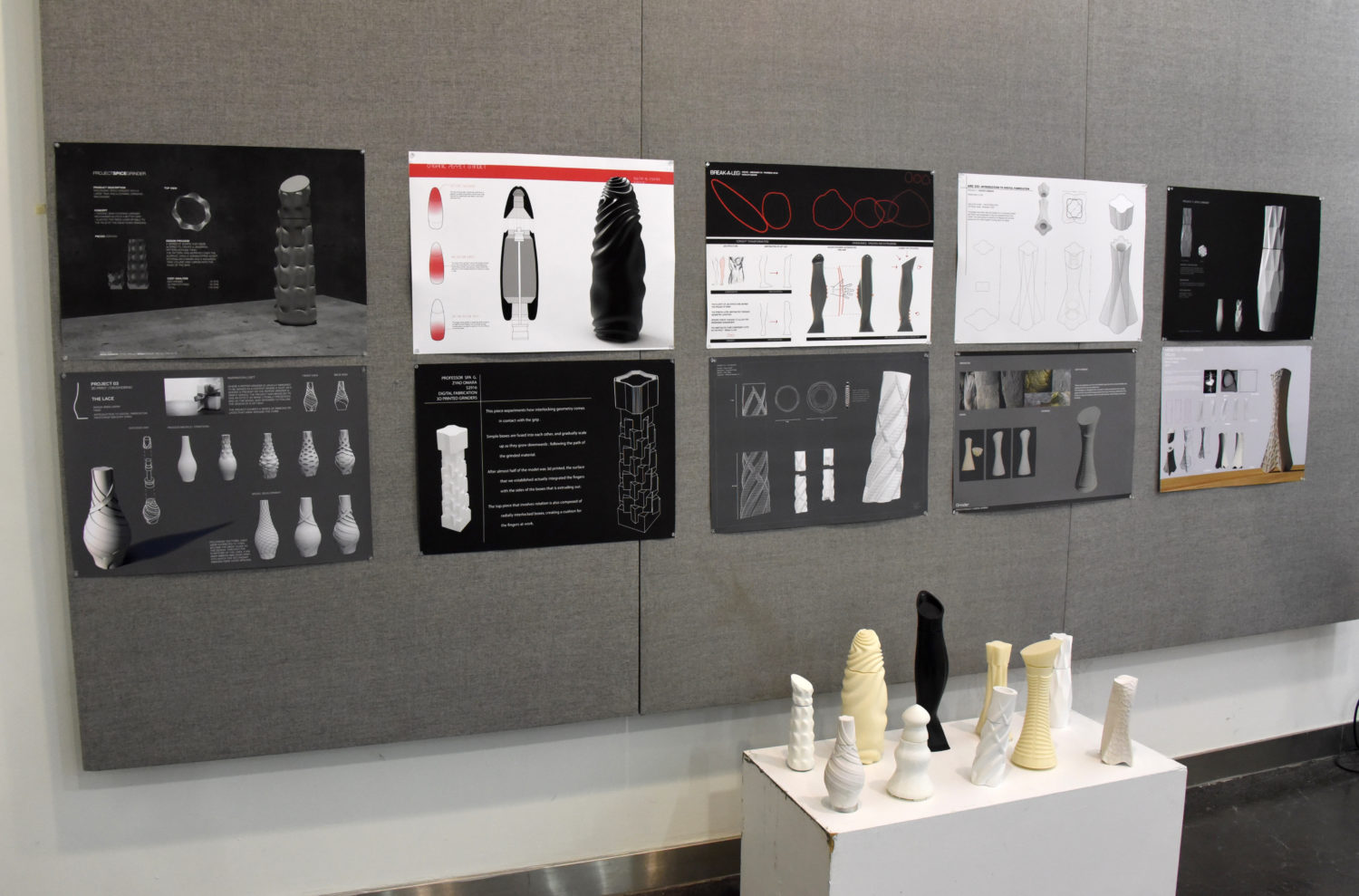
Project Three – Spice Grinder
Project 4: Tile
With a slightly longer duration, the fourth assignment allows students to familiarize themselves with a series of techniques and new pieces of fabrication equipment. Asked to create a tile or series of tiles that employs depth and continuity, the students translate digital models to the 3-axis CNC router via Mastercam. The students explore and take advantage of the software’s ability to customize tooling paths. As a result, the derived MDF master molds embody varying visual and haptic qualities related to the tool’s mechanical craft. To ease the production of numerous tiles, the school’s industrial thermoformer is used with the milled master mold to form a series of styrene molds. Using these, a field of cement or plaster tiles with high quality surfaces can be quickly poured.
What were the biggest takeaways you had from the course?
GS: At the conclusion of each assignment, beyond critiquing specific projects, the students and I discuss the successes and failures within the process and production of the final products. They articulate difficulties ranging from material limitations to hiccups with the fabrication equipment. At the same time, they are excited to see their designs come to fruition, indicating that their exposure to new programs, tools, and materials will be put to use in other aspects of their academic careers and beyond.
Are there any resources you would recommend for people who are interested in learning more or digging deeper into the Digital Fabrication realm?
Two books in Syllabus
- Iwamoto, Lisa. Digital Fabrications: Architectural Material Techniques. New York: Princeton Architectural Press, 2009. Print.
- Schodek, Daniel, et al. Digital Design and Manufacturing: CAD/CAM Applications in Architecture and Design. Hoboken: Wiley & Sons, Inc, 2005. Print.
Two more that you should check out:
- Thompson, Rob. Manufacturing Processes for Design Professionals. New York, NY: Thames & Hudson, 2010. Print.
- Dunn, N. (2012). Digital Fabrication in Architecture. London: Laurence King Publishing.
Online resource for scripts
David Rutten’s video tutorials on www.grasshopper3d.com are a good introduction for students who are interested in learning visual programming in support of their computation and digital fabrication projects. Beyond the primers in the tutorials portion of the site the the blog post and the corresponding community discussions are a critical forums for learning.
Food4Rhino (http://www.food4rhino.com) is a great resource for a potpourri of additional Rhino and Grasshopper Plug-ins.
Who should the readers follow on Instagram?
Nervous.system (Nervous System)
Softlab.nyc (SOFT lab)
Dwayneoyler (Oyler Wu Collaborative)
Ball_nogues_studio (Ball Nogues Studio)
Anything you would like to share with our audience. Words of encouragement, cat video, etc.
GS: Engage with technology and making is fun!
Check out University of Sharjah on StudyArchitecture.com!
https://studyarchitecture.com/school/american-university-of-sharjah/